Cross-Docking: Meaning, Process & Benefits Explained
Blogs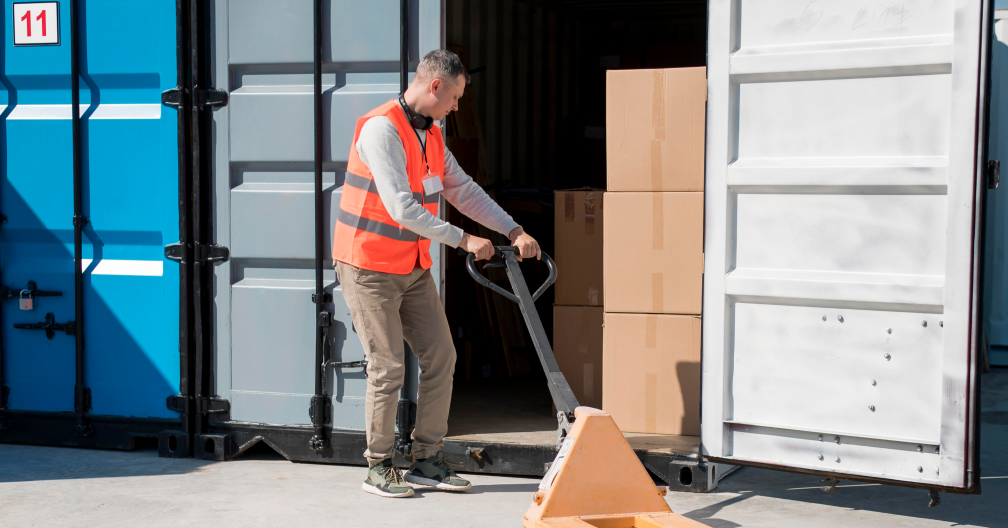
Can your business keep pace with the relentless demand for instant gratification? Today’s customers are quick to shift gears when delivery times drag, McKinsey shares, with over 90% of online shoppers expecting free two- to three-day shipping. This starkly illustrates the need for leaner operations and rapid fulfillment — which is why cross-docking has emerged as a dynamic solution, accelerating deliveries through a seamless flow of incoming and outgoing goods. While it may appear complex on the surface, its core principles are simple: minimizing storage and optimizing transportation.
In this blog, we’ll break down the ins and outs of cross-docking, covering everything from its fundamental definition and diverse variations to cross-docking advantages and disadvantages, so your business is equipped for successful implementation.
What is Cross-Docking?
When discussing supply chain efficiency, it’s important to understand the cross-docking meaning. Cross-docking is a logistics technique designed to slash delivery times and boost supply chain efficiency. It’s about orchestrating a seamless flow of goods: inbound shipments, typically sent by suppliers directly to a cross-dock warehouse, are immediately transferred to outbound vehicles.
With this dynamic practice, trucks are essentially acting as a relay, swiftly exchanging inventory without pausing for storage. This method, available in various forms, drastically cuts costs by eliminating unnecessary handling and prolonged storage, all within a facility designed for quick order consolidation and dispatch.
How Cross-Docking works
Building on the cross-docking definition, let’s take a closer look at this approach in action. Cross-docking in warehouse management operates through a rapid-transfer approach, breaking down traditional warehousing into smaller, agile tasks for quicker dispatch to retailers.
Consider a distribution facility, either managed in-house or by third-party logistics (3PL), receiving inbound shipments from multiple suppliers. Upon arrival, goods are immediately unloaded and sorted based on pre-assigned destinations. Facilitated by real-time tracking systems, items are then directed to designated staging areas where they are consolidated with other orders destined for similar delivery routes, enabling immediate transfer to outbound vehicles.
For example, time-sensitive goods like fresh produce or pre-sorted retail orders are efficiently moved from inbound to outbound docks, minimizing handling and accelerating delivery. Cross-docking relies on precise coordination and comprehensive inventory management to maintain a seamless flow, converting a complex distribution network into a highly efficient delivery system.
Types of Cross-Docking
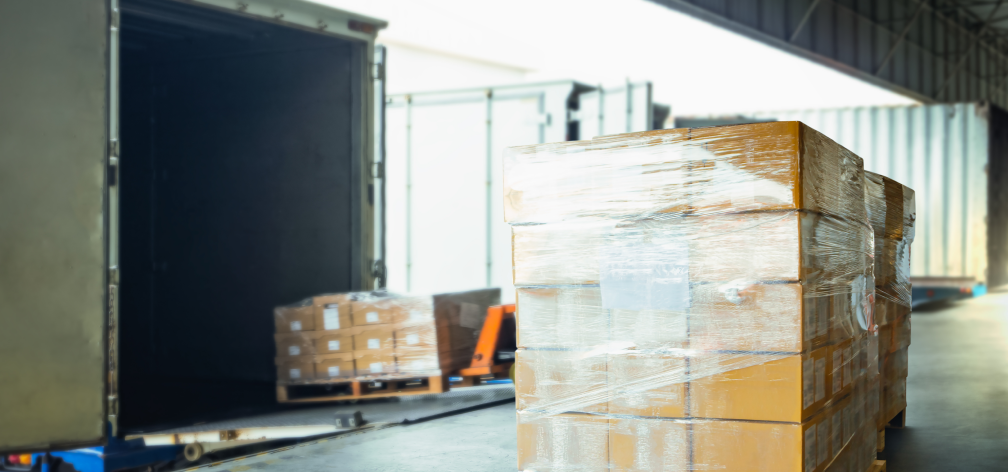
As e-commerce evolves, cross-docking is increasingly replacing traditional distribution models. Here are two primary cross-docking types that cater to different supply chain needs:
Pre-Distribution Cross-Docking
This method leverages predetermined destination data. Suppliers identify the final recipient of each product before shipping to the cross-dock warehouse. Once the goods arrive, they are immediately unloaded, sorted, and potentially repackaged according to these pre-set distribution instructions. This approach, characterized by minimal storage and handling time, is ideal for scenarios where demand is predictable and inventory allocation is known in advance.
Post-Distribution Cross-Docking
On the other hand, post-distribution cross-docking allows for destination flexibility. Goods reach the cross-dock without pre-assigned destinations, providing suppliers with a window to analyze demand and allocate inventory accordingly. While this results in slightly longer dwell times compared to pre-distribution, it offers valuable adaptability, particularly in fluctuating markets or when demand forecasting is challenging.
Benefits of Cross-Docking
Cross-docking offers a strategic advantage by significantly enhancing supply chain efficiency and reducing operational costs. Beyond accelerated shipping, this approach directly impacts inventory management, product integrity, and transportation expenses. Key benefits include:
- Accelerated Delivery Time: Cross-docking dramatically shortens delivery timelines by minimizing or eliminating warehouse storage. This rapid throughput is crucial for businesses facing heightened customer expectations for swift order fulfillment, particularly in retail sectors.
- Minimized Inventory Costs: By avoiding long-term storage, cross-docking substantially reduces expenses associated with warehousing, including storage fees, labor, security, and insurance. The elimination of prolonged inventory holding translates to direct cost savings and improved capital utilization.
- Reduced Risk of Product Damage: Minimizing handling and storage significantly lowers the risk of product damage. For perishable goods, cross-docking mitigates the risk of spoilage or expiration by ensuring rapid transit, preserving product freshness and quality.
- Optimized Shipping Costs: Cross-docking facilitates efficient load consolidation and deconsolidation, enabling businesses to optimize vehicle utilization. By combining or splitting shipments based on destination and volume, companies can reduce transportation costs and enhance delivery efficiency.
Challenges & Limitations of Cross-Docking
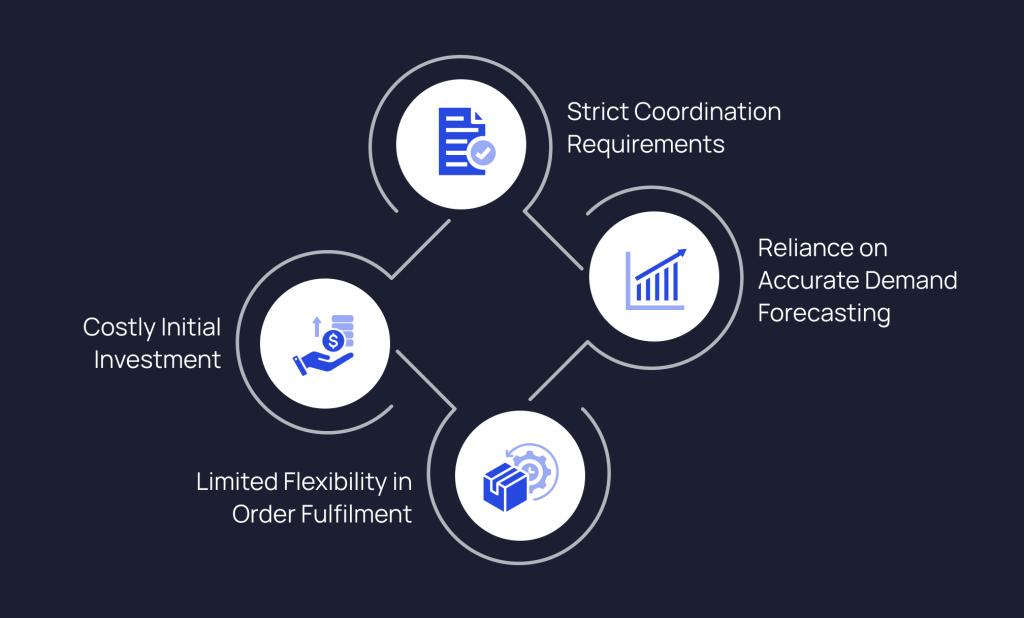
While cross-docking offers significant advantages, successful implementation demands careful consideration of inherent challenges. Establishing and maintaining efficient cross-docking operations requires strategic planning, substantial investment, and meticulous coordination. Review the following limitations:
- Costly Initial Investment: Implementing cross-docking requires substantial capital. The setup usually includes establishing cross-docking terminals, procuring outbound transportation, and investing in advanced warehouse automation technologies, such as robotics and sensor systems, to ensure seamless operations and real-time tracking.
- Strict Coordination Requirements: This approach relies heavily on precise coordination across the entire supply chain. Ensuring timely inbound deliveries from suppliers and securing adequate outbound carrier capacity at the exact moment of arrival is critical. It requires robust communication and advanced warehouse management systems to prevent scheduling conflicts and operational disruptions.
- Reliance on Accurate Demand Forecasting: Precise demand forecasting can make or break effective cross-docking. Miscalculations in product volume may lead to stockouts, as the system minimizes or eliminates buffer inventory. Therefore, reliable forecasting is crucial in maintaining a consistent flow of goods and meeting customer demand.
- Limited Flexibility in Order Fulfilment: As cross-docking is optimized for rapid deliveries, it is not well-suited for businesses requiring long-term storage or frequent, last-minute order modifications. Once goods are loaded onto outbound trucks, changes become difficult, limiting the system’s flexibility in accommodating dynamic order adjustments.
Cross-Docking vs. Traditional Warehousing
With a better grasp of cross-docking advantages and disadvantages, we can now examine how it contrasts with conventional warehousing. The main distinction essentially lies in how goods are handled within the facility. For a clearer look at their key differences and operational characteristics, here’s a comparative overview of cross-docking and traditional warehousing:
Features | Cross-Docking | Traditional Warehousing |
Storage time | Minimal to none; immediate transfer | Extended periods; days, weeks, or months |
Inventory levels | Low or no on-hand inventory | High levels of stored inventory |
Operational speed | Fast; immediate transfer from inbound to outbound vehicles | Slower; dependent on storage and retrieval |
Overall costs | Lower storage costs, potentially higher coordination costs | Higher storage costs, potentially lower coordination costs |
Flexibility | Limited flexibility for last-minute changes | More flexibility for storage and order adjustments |
Suitable for | Time-sensitive goods, predictable demand | Diverse product types, fluctuating demand, long-term storage |
Primary goal | Speed and efficiency in product flow | Storage and inventory management |
Implementing Cross-Docking in your Business
Successful cross-docking in warehouse management relies heavily on thorough planning and flawless execution. Businesses looking to adopt this logistics approach should consider the following action steps:
- Strategic Product Selection
Begin by pinpointing products with consistent, high-volume demand and short shelf lives. This is to ensure they move quickly through the cross-dock, minimizing storage and maximizing efficiency.
- Facility and Layout Optimization
Designate dedicated dock doors for incoming and outgoing shipments, alongside a streamlined cross-docking area with efficient pathways to minimize handling and movement time.
- Technology Integration
Integrate an advanced Warehouse Management System (WMS) to enable real-time tracking, optimized scheduling, and seamless data exchange across the supply chain. This technology provides a solid foundation for businesses to scale logistics and fulfillment.
- Process Development and Testing
Develop detailed Standard Operating Procedures (SOPs) and clearly define responsibilities to promote consistent and effective execution of the cross-docking process. To prevent potential issues, run pilot tests to ensure operational efficiency.
- Supplier and Carrier Collaboration
Strong communication with suppliers and carriers is vital for seamless cross-docking. Ensuring adherence, for example, to strict delivery schedules and labeling requirements is a key driver of operational efficiency.
- Performance Monitoring and Optimization
Continuously monitor KPIs and analyze data to identify areas for improvement. By regularly refining these processes, businesses can strive for optimal cross-docking performance.
Conclusion
In short, defining what is cross-docking is the first step towards transforming your supply chain. This strategic logistics model helps businesses move beyond traditional warehousing constraints by minimizing storage, accelerating delivery, and significantly reducing operational costs. Understanding the nuances of its core processes, including the various cross-docking types, is necessary for businesses aiming to optimize their operations.
Advanced solutions like Anchanto’s Control Tower further enhance supply chain visibility, enabling businesses to tailor cross-docking implementation, boost efficiency, and improve customer satisfaction in today’s demanding market. To learn more about cross-docking and how to improve your supply chain logistics, get in touch with our experts today.